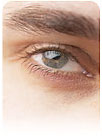
Non-compliance with emergency eyewash safety standards is a serious issue in today’s workplace. According to the National Institute for Occupational Safety and Health (NIOSH), this lack of compliance contributes to a reported 2,000 injured U.S. workers each day. In fact, the U.S. Bureau of Labor Statistics (BLS) reports that eye injuries lead to 37,000 missed days of work and more than $300 million per year in related costs.
A large part of the problem is that many companies simply do not understand the need for emergency eyewash stations in their facilities. Taking the proper steps to ensure compliance before an accident occurs is a proactive first step that companies can take to protect employees’ eye health.
Education & compliance
Lack of first-aid eyewash/emergency shower facilities ranked fifth on OSHA’s 25 most-cited general industry violations in 2005. Though reasons for this number may vary, employers’ lack of understanding is a major factor. As a rule, laboratories or companies require eyewash stations if work areas include paint, solvents, battery charging stations, hazardous chemical storage, tool parts washers or chemical pumping/mixing areas. If employees are using chemical-resistant gloves, cartridge or air-supplied respirators, chemical-resistant goggles or flammable storage containers, eyewash protection is likely required as well.Although OSHA sets the overall requirement that employers provide eyewash stations, it refers to the American National Standards Institute (ANSI) to guide employers in establishing and maintaining work practices relating to eye safety. Specifically, ANSI standard Z358.1 requires eyewash stations:
For specifics on OSHA and ANSI requirements, companies should refer to OSHA Standard 1910.151, titled Medical Services and First Aid, and the ANSI Z358.1 Standard for Emergency Shower and Emergency Eyewash Equipment.
Eyewash stations: Know the options
There are two styles of eyewash stations available — each with different features and implications for eye health. Companies should do their research to learn the pros and cons of each system and to make informed decisions when choosing a station. Current eyewash station options include plumbed and portable units. Portable units can be further classified as tank-style or sealed-fluid cartridge stations.Plumbed eyewash systems are permanently connected to a source of tap water. Their greatest attribute is the ability to deliver plentiful amounts of flushing fluid. Of course, it is better to flush with tap water than not to flush at all, but medically it is not the optimal solution. Not only does tap water not match the pH of the eye, but it could also contain contaminants and microorganisms — both of which could further irritate and injure the eye, and potentially lead to serious complications such as corneal cell damage. Additionally, untempered tap water may be too cold or too hot, making it uncomfortable to rinse the eyes continuously for the required 15 minutes. Because these stations must be connected to fixed plumbing, they are expensive to install and impractical to move. They also require weekly flushing maintenance.
Portable, tank-style eyewash units contain their own flushing fluid and do not require fixed plumbing. The solution in the tank-style unit can be either a mixture of water and preservatives, or water plus a buffered saline mixture to help ensure safe flushing. They must be cleaned and refilled in accordance with the manufacturer’s instructions; however, this only needs to be done every six months. Because these stations are not connected to fixed plumbing, they can be moved, easily enabling companies to adapt quickly to changing work environments or locations.
Portable, sealed-fluid cartridge devices represent a major step forward in workplace eye injury treatment. Leading units feature factory-sealed cartridges containing a purified, buffered saline solution that remains free of bacteria or contamination for 24 months. This two-year shelf life is determined by the date of manufacture, and is more than four times longer than any other primary, portable eyewash station. The units can only be refilled with a sealed-fluid cartridge, thus avoiding the contaminants found in tap water.