Maintaining clean air in the workplace is crucial for safeguarding employees’ health, especially when it comes to dust generated by manufacturing processes. Employers must comply with safety regulations that mandate the prevention of workplace hazards that could result in injury or death, as outlined in the General Duty Clause of the OSHA Act of 1970.
Dust collection systems are often the most cost-effective method of removing toxic and combustible dust. These powerful systems play a key role in regulatory compliance.
Dust collectors work by pulling in particles from the air, filtering out the dust, and then circulating the purified air back into the workspace or releasing it outside. This process effectively minimizes dust accumulation on surfaces and prevents workers from inhaling harmful particles.
To ensure that the correct dust collector is specified for an application, two important steps are required. First, analyze the dust to understand its properties. Second, apply ASHRAE standards to evaluate and select the required filtration.
#1: Test your process dust
Understanding dust and its characteristics is key to determining the best dust collection system and filters for an application to remain compliant with indoor air quality standards. Your air quality management plan should set objectives in line with ‘Industrial Ventilation: A Manual of Recommended Practice for Design’ by the American Conference of Governmental Industrial Hygienists (ACGIH). Additionally, it’s important to comply with OSHA’s prescribed exposure limits for the dust that is generated by your specific operations.
As of 2020, the National Fire Protection Agency (NFPA) requires a documented dust hazard analysis (DHA) in accordance with NFPA 652: Standard on the Fundamentals of Combustible Dust. This analysis is crucial for identifying potential dust-related explosion and fire hazards and can help determine if the dust affects indoor air quality.
When to Test Dust
Dust testing is essential when installing a new dust collector system, starting a new manufacturing process or when the facility has been generating and capturing the same type of dust for an extended period. Changes in equipment, processes, environment or products can affect dust characteristics.
If a dust collector works too hard, uses too much energy or does not operate effectively, it might not be configured properly for the application. The dust characteristics analysis and the DHA provide the information needed for the supplier to configure the ideal system. This includes the size of the filter housing, the design of the ductwork and the hopper/dust discharge setup. When configured appropriately, the system will operate more efficiently, saving energy, reducing compressed air usage and enhancing air quality.
A dust analysis also helps in choosing the right filters for the dust collector. The type of media used in a filter cartridge to collect and trap airborne particles is based on dust characteristics and the application process. For example, dusts like crystalline silica and hexavalent chromium are hazardous to human health and require high-efficiency filters that meet OSHA requirements. Dust generated from food processing applications may be moist or sticky and benefit from washable polyester filter media.
A dust analysis can recommend what type of filters should be used in dust collectors, helping them to better filtrate respirable dust that can affect worker health.
Dust testing basics
To identify the properties of dust, facilities can utilize a testing laboratory that uses specialized techniques and equipment to determine particle traits such as size and shape, gravity effects, moisture level and abrasiveness. Combustible dust testing should be performed by an accredited lab with the proper equipment per NFPA requirements.
Data provided by dust sample bench testing provides a better understanding of the physical properties of your dust, which forms the basis for equipment selection or modification.
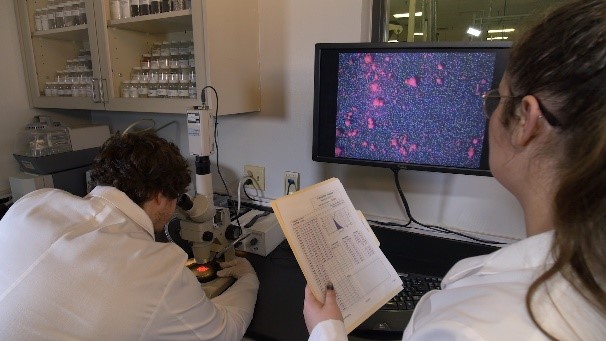
Dust testing laboratory
Collecting dust for analysis
When collecting the dust sample, first review the material’s safety data sheet to take the right precautions against any hazards associated with the dust. If there is an existing dust collector, a dirty filter provides an ideal sample. Otherwise, collect a sample that represents the dust for capture by the collector. Dust swept from the floor could contain impurities and other materials. Dust from a hopper is not recommended because the sample will not represent the true particle size distribution of the dust captured by the filters. The testing lab can provide guidelines on proper sample collection.
Types of dust tests
As noted, a testing lab will conduct a variety of tests to determine the following:
Particle size
A test lab can determine dust particle size down to the submicron range. Particle size determines the filtration efficiency required to meet emissions standards noted in an air quality program and the DHA and to comply with OSHA regulations. A dual‐laser particle analyzer pinpoints the count (number of particles of a given size) and volume or mass spread of the dust. Because many dusts are composed of a mix of submicron and larger particles, knowing the count and volume is important for selecting the appropriate filter media to ensure indoor air quality.
Particle Shape
A test lab will use an optical microscope to observe the shape of dust particles while using a scanning electron microscope to obtain detailed media images. The data is combined with the particle size analysis to help determine what type of dust collector and filters are best for collecting a dust type.
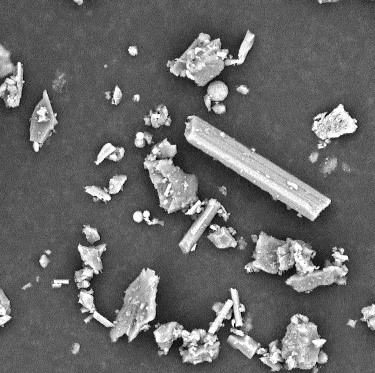
Magnified silica dust particles
For example, if a test reveals a crystalline structure with jagged edges like fumed silica, this toxic dust will require a high-efficiency filter that is chemically treated with an additional layer of nanofibers or PTFE. Microscopic analysis also can identify oil in the dust, which can cause serious problems with dry dust collectors and require the use of a filter media with an oil‐resistant coating.
Abrasion
Understanding dust abrasiveness helps determine the optimal design of dust-handling components including inlets, baffles, discharges and ductwork. For example, when capturing highly abrasive dust like cast iron grindings, a collector must be designed with low inlet velocity. If the inlet velocity is too high, the dust will abrade the filters and cause premature wear.
Moisture
If dealing with moist dust, early detection is important in selecting the proper filter media. Test labs use a hygrometer to identify the presence of moisture in the dust. This helps to determine collector design elements like hopper angle and conveying velocities. Moisture problems also could affect filter performance, as sticky dust can cause plugging up of filter cartridges with the wrong type of media.
#2: Select filtration using ASHRAE standards
In addition to dust analysis, air filtration and dust collection standards set by the American Society of Heating, Refrigerating and Air-Conditioning Engineers (ASHRAE) can help in selecting the right dust collector filter cartridge.
ASHRAE standards and guidelines provide uniform methods of testing filter efficiency, recommend practices in designing and installing equipment, and deliver additional information on industry best practices.
ASHRAE Standard 52.2
ASHRAE 52.2 outlines a test method and MERV (minimum efficiency reporting value) rating system to determine a filter’s efficiency in capturing dust within specific size ranges. The MERV ratings outline filter efficiency on a scale from 1 to 16 according to a filter’s ability to capture particles in a range of 0.3 to 10 microns. The higher an air filter’s MERV value, the greater the percentage of particles it can capture on each pass. A filter rated as a MERV 14/14A filter, for example, should remove at least 75 percent of all particles larger than 0.3 microns, while a MERV 16/16A filter should remove 95 percent.
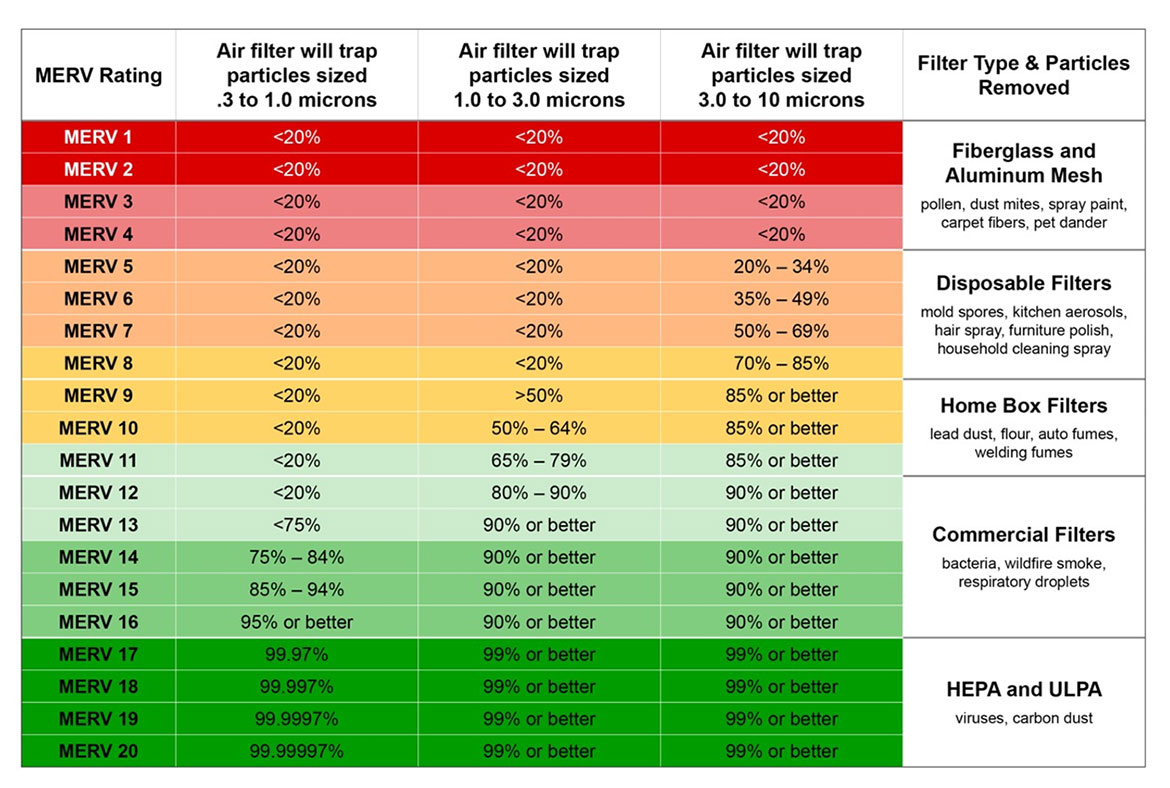
MERV rating, filter type and particles removed
Use MERV Ratings for HVAC filters, not dust collector filters
While MERV ratings are helpful in selecting HVAC air filters, they are not as useful for evaluating industrial dust collector filters, even though many replacement dust collector filters provide MERV ratings. This is because MERV ratings apply to the initial filtration levels of new filters in a static environment. Typically, these filters are not designed to release dust and are replaced when loaded with particulates. However, dust collector filters are used over a long period of time in a very active system. They also handle more challenging dust types and loads than HVAC filters. In addition, they undergo repeating cycles of dust accumulation and pulse cleaning. Because of these aggressive factors, the efficiency of dust collector filters fluctuates.
These dynamics are not considered in a MERV rating. Although MERV identifies an air filter’s pressure drop (resistance to airflow caused by dust accumulation), it does not address overall energy usage that significantly changes throughout filter life. With higher airflow restrictions, more energy and compressed air are needed to maintain the proper airflow and pressure drop in the dust collector.
A better standard to test dust collectors
ASHRAE Standard 199 Method of Testing the Performance of Industrial Pulse Cleaned Dust Collectors specifically addresses the dynamics of dust collectors versus HVAC systems. Prior to Standard 199, Standard 52.2 was the only filtration test available for dust collection.
The Standard 199 test method calculates the performance of the industrial pulse cleaned dust collector, including filtration performance and energy consumption. It assesses the unit from inlet to outlet and how well the filters are cleaned. Results from Standard 199 testing indicate if the dust is releasing properly from the filters as well as the longevity of filter life. It should be used to determine system design and filter media selection.
Testing challenges the dust collector to replicate real-life use. It uses calcium-carbonate dust with specific particle size, bulk density and moisture content, as stipulated in the standard. The methodology includes six stages:
Stage 1: Initial dust loading. Dust is fed into the collector at the specified rate, without pulse cleaning, until the system reaches the required differential pressure.
Stage 2: Initial dust loading with on-demand cleaning. On-demand pulse cleaning is initiated while dust continues to be fed into the collector at the same airflow. The high and low differential pressure set points determine the cleaning interval.
Stage 3: Dust loading with continuous cleaning. Airflow and dust feed are maintained, and pulse cleaning of the filters continues at regular intervals for 24 hours or until the system reaches the specified maximum differential pressure.
Stage 4: Final dust loading with on-demand cleaning. The final dust loading is tested with on-demand cleaning, and airflow and dust feed are maintained. As with Stage 2, the high and low differential pressure set points trigger the filter cleaning. The frequency of cleaning varies depending on the system’s performance and pressure buildup.
Stage 5: Upset condition. Dust feed is maintained, and pulse cleaning is stopped to simulate how the dust collector would perform in an upset condition.
Stage 6: Post-upset condition. The cleaning process downtime is replicated to imitate a post-upset situation and return to normal system operation.
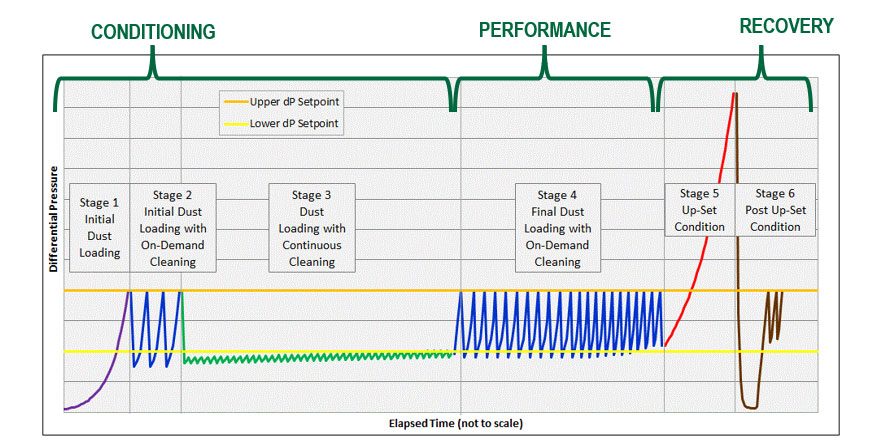
Image: ASHRAE Standard 199 Testing Stages
Bottom Line
Effective dust management is crucial for indoor air quality and staff health. Dust testing is a key part of this effort because understanding particle types helps determine the best equipment and filtration to capture them.
Secondly, you must understand how to select the most efficient dust collector filter cartridges. MERV ratings, commonly used for HVAC filters, may not accurately represent the conditions in dust collection systems. ASHRAE Standard 199 offers a better assessment of dust collectors and filters by simulating real-world conditions.