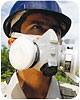
The law requires your company to have a written respiratory protection program (RPP) that, depending on your location, addresses the following “obvious” requirements:
- OSHA 29 CFR 1910.134, Respiratory Protection and other regulation-specific standards.
- NIOSH guidelines and certifications of respirators.
- Canadian Standards Association Z94.40-02, Selection, Use and Care of Respirators and other regulation-specific standards.
What are these “not-so-obvious” requirements?
Safety culture is the “not-so-obvious” component of a strong RPP. It may be reflected, for example, in the degree to which respirators are used when requirements are not clearly determined. A case-in-point is full-filtering facepiece respirators with an N95 rating that must be worn for potential exposure to airborne diseases. Should they also be worn as a precaution when the disease or transmission status has not been verified? If the answer is yes, this demonstrates a positive safety culture and an effective program.
What steps should an organization take to address their “not-so-obvious” safety culture requirements? The following suggestions will help you get started in evaluating your program.
Provide hands-on training
At the time of training, are employees simply given the manufacturer’s directions and asked to read them, or are they given hands-on instruction? Remember that adults learn by doing, and training in this way takes time and dedication on the part of the trainer.
Talk to employees during training and fit testing to ensure proper donning and removal of PPE, and make sure they understand the relevant terminology. The whole training process is about building trust and comfort, so ensure that your training has a personal touch and is not conducted in groups too large to allow for ease of interaction.
Emphasize the employee’s role in each aspect of training, including user seal-checks over the actual fit-testing procedure. At the same time, it is important to get a feel for all hazards that may be present, such as corrosives that can cause harm to the skin and eyes that may not have been previously assessed.
Be sure to provide RPP training for managers and supervisors who have responsibility for the safety of their employees. An observation checklist is a specific, measurable tool that can document compliance or performance before problems occur.
Develop a system to document an employee’s understanding of respiratory protection. A test for each type of respirator that references limitations, uses, cartridge change-out, storage etc. must be used and kept on file along with records of fit testing and medical certification if required. This ensures that employees are thinking about how to use, store, clean and dispose of their respirator.
Finally, there is an element of salesmanship involved in all training, and the trainer must assess the needs of the audience and train accordingly.
Address employee concerns and misconceptions
Respiratory protection is the last line of defense against hazards such as microorganisms and airborne toxins that may not have clear warning properties. It is important to have explanations and scientific data available that the trainer/fit tester can convey to employees in an understandable, simplified way.
Two common concerns, for example, are whether or not to be clean-shaven when wearing a respirator and whether or not to pull long hair back from the face to avoid inward air leakage if hair gets caught in the respirator. In these situations, let employees understand why a seal is required; explain the miniscule size of particles and molecules and how they follow the path of least resistance around — and not through — respirators. It is also important to have knowledge of air sampling and exposure data to explain related hazards to employees.
Fit testers/trainers need to be experienced enough to deal with other common questions and concerns that arise about the toxicity of test agents. Some of these include fogging of eyeglasses, irritancy of skin, build-up of carbon dioxide, breathing resistance, use of respirators and concerns about pregnancy etc.
Finally, try to assess confusion and provide clarification regarding your company’s “lingo.” For example, in the hospital environment there may be a tendency to make little distinction between surgical masks and respirators — employees need to know the difference.
Assure quality of fit testing
Provide flexibility in time and location of fit testing, and use a variety of media for announcing and scheduling fit-testing sessions. It is important for employees to feel comfortable during this process, so be sure to chat with them in order to help them feel relaxed. Provide a number of fit-testing agents for qualitative fit testing in case of sensitivities, and note that quantitative methods will need to be used in some cases.
Let each employee be part of the decision-making process for the type of respirator to ensure his or her buy-in. Ask about preferences and offer a variety of sizes and designs. This is necessary, not only to accommodate different sizes and shapes of faces, but also to take into account the many concerns that may arise.
Maintain detailed records
It is very important for managers and employees to have ready access to respiratory protection data for each employee including:
- the respirator and cartridge required;
- the date of the last training/fit testing completion;
- the department worked and its occupation and potential hazards;
- any unique requirements for fitting of the respirator;
- the employee’s health status;
- the type of fit test conducted.
Budgeting for the time required to input data and for the IT resources to keep this information up-to-date and accessible is a must. Note that other departments such as purchasing/stores/inventory control will need this information for inventory, but also for pandemic planning purposes.
Have supplies readily available
Ask employees at the time of training/fit testing if they have access to the specific respirator required in their department as well as to proper cleaning solutions, cartridges etc. You may have to get directly involved in the purchasing process in many circumstances. Be certain that your managers’ training covers this topic.
Have a qualified RPP administrator
Managing a program takes an enormous number of resources, so it is important that your RPP administrators have the credentials and background necessary to implement and oversee your program, as well as to give it credibility. Someone with the necessary experience, accreditation and certification in occupational health and safety will be able to address the employees’ needs as well as the legislative requirements.
The administrator must regularly review the program components, and have access to up-to-date research. From my perspective, the NIOSH Personal Protective Equipment Research studies and the Journal of Occupational and Environmental Hygiene can be great resources. The administrator must also regularly review new products and the relevant legislative and guidelines changes.