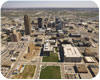
Starting in the 1970s and continuing into the 90s, the concept of industrial parks spurred the imagination of city planners and businesses alike. Soon industrial parks started popping up faster than onion sprouts in the valuable agriculture land the parks displaced. In theory the parks were developed to move industry to the outskirts of the city, allowing more urban green space. Often these parks are located close to interstate highways, rail transportation, and airports to promote more efficient and faster shipment or goods and supplies.
Parks also allowed for the concentration of infrastructure in a dedicated area, helping to reduce the cost of high-powered electric supply, high-end communications cables, and large volume water and gas supply lines. Most parks are occupied by light to medium manufacturing facilities, the same types of businesses already struggling with regulatory compliance.
Industrial parks offer a plethora of economic advantages that go unrealized simply because no one group or person has general oversight of the community. Industrial parks are essentially neighborhoods without associations. With just a little bit of creativity, planning and organizing, the American industrial park could reach its imagined potential by maximizing resources like public transportation for employees, bulk shipments, shared talent of specialized human resources, bulk hazardous waste removal; the list is limited only by the imagination.
Captive audience
Recently, health authorities in India saw a need to educate the populace about HIV/AIDS in the quickest time available. They started holding classes in the industrial parks around the surrounding communities, rationalizing that industries provide an excellent audience of mature men and women within a cross section of the community. Adult learning centers located in an industrial park became a novel idea.
Here’s another reason for industrial park neighbors to band together and share safety programs and risk assessments: OSHA will be coming on stronger thanks to the new administration’s embrace of many of organized labor’s agenda items, including tough safety and health standards enforcement. More field inspections and inspectors; more regulations such as the long debated ergonomics standard, as well as new standards covering cranes and derricks, combustible dust, beryllium, silica, and hazard communication to incorporate the Globally Harmonized System of Chemical Labeling are expected. Action will pick up once OSHA’s new leadership team settles in in 2010.
In May of 2009, OSHA sent out letters to more than 13,500 employers nationwide informing them that their injury and illness rates are considerably higher than the national average. This notification was a proactive step to encourage employers to take positive action to improve safety and health conditions in their workplaces. OSHA encourages these employers to utilize the services provided by OSHA, or employ outside safety and health consultants to help improve their incident rate. Although most businesses see health and safety as a core business value, they also see spending money on consultants during our lethargic economy almost as abhorrent as inviting OSHA onto their premises. Nevertheless, those that ignore OSHA’s “suggestion” do so at their own peril.
Safety learning centers
The question arises: What if industrial parks were to co-opt safety consulting and training, and established safety-learning centers within the confines of the community?
According to “Commercial Real Estate in a Flat World: The Implications of Corporate Restructuring and Economic Globalization for Industrial, Office and Mixed – Use Property in America”, a report submitted to the National Association of Industrial and Office Properties (NAIOP) by consulting futurist David Pearce Snyder: “…communities that offer dynamic, multi-dimensional places in which to live, work and play will be better able to attract and retain the next generation of scarce, high value-adding employees… and their employers.”
Community approach to safety
What might be some of the advantages of cooperative safety consulting and training? One of the benefits could be the coordination of emergency action plans both for individual facilities and for the complex as a whole. OSHA requires that each facility with ten or more employees have written emergency action plans (CFR 1910.38). The plans must cover actions that designated employers and employees are expected to take to ensure employee safety from fire and other emergencies. The plans are required to identify potential emergencies and convey to employees just what their responses should be.
But a manufacturer at one facility may think the scenario for a risk factor highly improbable at his facility without realizing that the risk is highly probable at another facility less than 50 yards away! Having a shared safety consultant who sees the overview of the whole complex could prove to be invaluable over time.
Each facility is required to have its own hazard communication program (HazCom). It must be a formal, written program (1910.1200) requiring the employer to access the chemical hazards in the workplace to which employees may be exposed. This information must be available to employees of all shifts whenever they require it.
Recently there was a story of a trucking company in the Green Bay area that preloaded refrigerated trailers and staged the trailers along a chain-link fence separating their property from the neighbor’s facility. Unfortunately, the staging area was right under the neighbor’s intake opening for their air make-up unit. The carbon monoxide created by the operating refrigeration units was sucked into the vent, exposing the employees inside the building to high levels of carbon monoxide and making them sick. Having central oversight of all facilities in the complex might have prevented this potentially serious incident.
Centralization benefits
Another advantage of co-opting is that it allows for easy make-up sessions for employees who are absent on training day. These employees can simply attend a make-up session at a neighboring facility. Co-opting also provides extra safety experts during catastrophic events, provides accident investigators when needed, and can provide supplemental safety and environmental resources for those establishments that employ their own environmental health and safety professionals.
Even though our economy is struggling, there is little doubt that OSHA is going to be more aggressive in the enforcement of safety and health regulations in this administration. Those employers who think creatively and economically will be the employers who prosper, and who keep their employees the safest.