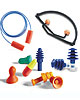
Training programs are often defined by what they teach, not what is learned. That difference between knowledge and application plays itself out in every hearing conservation program. Many of our noise-exposed workers seem to be saying to us, "Oh, I know all that stuff about noise, but I just don't care. It just doesn't matter."
This attitude plays out in hearing protectors that are worn for show, not for protection. It's not uncommon for safety managers to have 100 percent compliance in noise hazard training, and 100 percent compliance in use of hearing protection, yet still see increasing rates of noise-induced hearing loss (evidenced by OSHA Standard Threshold Shifts) among workers.
Where is the disconnect?
Attitudes toward hearing conservation
In a comprehensive 2002 study, the Institute of Occupational Medicine in the United Kingdom studied the human factor in hearing protection — worker attitudes, risk perception and behavior. UK researchers surveyed 280 workers at 18 companies across several industries. A separate survey was administered to the managers at those same companies to learn if workers perceive the hearing conservation program the same way it is perceived by managers.The biggest disparity appeared on the topic of training. At many worksites where employers had provided hearing conservation training, workers had little recollection of the training, or even denied ever receiving it.
- When hearing conservation training was provided at new-hire induction, only 27 percent of workers recognized they had been trained.
- When hearing conservation training had been provided by posters, only 46 percent of workers recalled any information from the poster.
- When training materials were in the form of a leaflet, only 39 percent recalled receiving training.
- Overall, at worksites where managers reportedly provided training in the use of hearing protectors, about two-thirds of the workers could not recall or recognize having been trained.
Training content
In the second phase of this UK study, researchers provided hearing conservation training at four selected facilities. Results showed that the effectiveness of hearing conservation training could be measured by two factors: content and method. In terms of content, the most effective training included the following:- audio demonstrations of noise-induced hearing loss
- actual examples of hazardous noise sources at work
- hands-on opportunities for workers to try different types of hearing protectors
- demonstrations of proper fit
In terms of training method, the most effective training was formal personal training, supplemented with audio and visual resources. Where companies relied heavily upon informal training, pamphlets or posters, the low impact of the training was evident: workers often could not recall the content, and personal protective behavior was lowest. But when noise-exposed workers underwent formal training, including audiovisual resources (audio demonstrations of hearing loss, for example), researchers found a 70 percent improvement in observed use of hearing protectors.
A lesson from optometry
The frustration of trying to convey knowledge that sticks, and help noise-exposed workers care about protecting their hearing, is not a new problem. In his hearing clinic in North Dakota, hearing clinician Dr. John Tongen has developed an effective solution.He describes how optometrists have an advantage over hearing clinicians. In a vision exam, it's immediately apparent which lines we can and cannot read. Because of this small interactive step, we don't need to wait until the completion of the exam for the optometrist to tell us if there's a problem. We already know we need corrective lenses
But a hearing exam is different. Typically, in a hearing test, only the audiologist is aware of the errors occurring during testing. Patients proceed through the entire test completely oblivious to their errors. In fact they can be downright incredulous when they are informed at the end of the test that they scored low.
Dr. Tongen's solution? In the sound booth, he places a computer monitor that displays large font text. As he reads his list of words in a speech recognition test, the patient responds with what he thought he heard, rightly or wrongly. Immediately after the response, Dr. Tongen displays the correct word on the monitor — and the patient knows right away if there is a problem. By the end of a 20-word list, the patient who has missed 12 words doesn't need much convincing there is a problem and that intervention is needed.
An effective training tool
Does hearing conservation have interactive training tools like this to deliver a more compliant noise-exposed worker to the training process?Absolutely.
The annual audiogram is a key tool. Research has shown that workers who receive immediate feedback following their annual hearing test (a copy of the audiogram and an explanation of their results) have lower rates of OSHA Standard Threshold Shifts (STS) in hearing.
We also have powerful tools now available to provide feedback in the fit and effectiveness of hearing protection — in essence, a fit-test for earplugs. This is not a new idea: the concept of fit-testing hearing protection has been around for a couple decades, but the methods have become significantly better, more accurate and more worker-friendly.
The benefits of fit-testing in a hearing conservation program are crucial to the success of the program. Fit-testing fulfills OSHA requirements to "ensure proper fitting" of earplugs and evaluate their attenuation. Fit-testing also documents the retraining and refitting required for STS-affected employees. After all, the mere act of giving a worker an earplug with a higher NRR gives no assurance that worker will obtain higher protection — that can only be measured with fit-testing.
In recent field studies among noise-exposed workers, fit-testing of hearing protectors has shown valuable results. In one study, the attenuation of noise-exposed workers at eight different companies was measured. Workers wore a variety of earplugs from several different manufacturers. Significant findings included:
- One-third of the tested workers achieved real-world attenuation that was equal to or higher than the rated attenuation (published NRR) for their respective earplugs. The middle third of workers achieved attenuation within 5 dB below the NRR, while the remaining third showed real-world attenuation anywhere from 5-30 dB below the NRR.
- The factor that showed the highest correlation to good earplug fit was the number of one-on-one training sessions the worker had received in fitting earplugs. Large group training in hearing protection seemed to have little effect; only individual training was correlated to high attenuation results.
Choice of earplugs
Fit-testing of earplugs also confirms the value of choice. Research in the field showed the following:- When new employees were given the choice of several different earplugs, only one-third initially chose their best-protecting earplug. For new employees, the "first choice" is often their "worst choice."
- Workers who achieve low personal attenuation ratings with one earplug often show immediate and significant improvement just by trying a different earplug.
- Sixty days following fit-testing using multiple earplugs, 80 percent of tested workers could recall the best-fitting earplug. Fit-testing results provided "sticky training" — training that made a behavioral difference in noise-exposed workers over time.