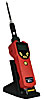
Worker exposure to benzene is a global problem. Benzene is a volatile organic compound (VOC), normally found in liquid form that is colorless, highly flammable and has a sweet odor. Today, benzene ranks in the top 20 in production volume for chemicals produced in the United States.
OSHA reports that as many as 238,000 people may be occupationally exposed to benzene in the United States each year. Industrial processes are the main source of benzene in the environment and it has been found in at least 1,000 of the 1,684 National Priority List sites identified by the United States Environmental Protection Agency (EPA).
Benzene is a recognized carcinogen and a developmental and reproductive toxicant. It is also suspected as a toxicant in cardiovascular, endocrine, gastrointestinal, immunological, neurological, and respiratory systems. Most people can begin to smell benzene in air at 1.5 to 4.7 parts of benzene per million parts of air (ppm) and can begin to taste benzene in water at 0.5 to 4.5 ppm.

Benzene’s health hazards
Short-term exposure to high doses (700 to 3,000 ppm) of benzene may cause drowsiness, dizziness, headaches, tremors, confusion, and/or unconsciousness. Death may occur after oral ingestion or inhalation of very high concentrations (approximately 10,000 to 20,000 ppm) of benzene.Tight exposure limits have been set as a result of these health effects (see Table 1 below).
Monitoring and measuring
OSHA has set forth regulations on the sampling and analytical methods for benzene monitoring and measurement procedures. There are a number of methods available for monitoring employee exposure to benzene, including portable direct-reading instruments, real-time continuous monitoring systems, passive dosimeters or other suitable methods.The employer has the obligation of selecting a monitoring method that meets the accuracy and precision requirements of the standard matching their unique field conditions. The standard requires that the method of monitoring must have an accuracy to a 95 percent confidence level, of not less than plus or minus 25 percent for concentrations of benzene greater than or equal to 0.5 ppm.
Conventional four-gas monitors make up the bulk of real-time monitoring in industry today. But because four-gas monitors typically only measure oxygen (O2), carbon monoxide (CO), hydrogen sulfide (H2S) and the lower explosive limit (LEL) of combustible gases, they miss many common toxic gases and vapors that are major constituents or by-products of industrial processes.
Benzene and harmful VOC monitoring
Each type of sensing technology has strengths and weaknesses, but PID, or photoionization detection, the first choice in detecting hydrocarbons, is frequently the optimal choice for real-time monitoring where benzene is present.Single-use gas detection tubes
Colorimetric gas detection tubes operate by drawing a gas sample through a tube filled with a reagent that changes color upon reaction with the chemical of interest. The length of stain is used to estimate the concentration of the chemical. They are an inexpensive and proven means of measuring many toxic gases and vapors at parts-per-million (ppm) levels. Most benzene-specific tubes use a combination of a pre-tube to filter out interferences connected to a measurement tube. The primary drawbacks to colorimetric tubes are: 1) Slow response, requiring multiple pump strokes and 5 to 20 minutes of manual sampling; 2) Readings are subject to interpretation and errors are ≥35% at 0.5 ppm; 3) The “spot check” nature of tubes makes them more prone to sampling errors due to small sample volume, air currents, or poor technique.Semiconductor or metal oxide sensors (MOS)
MOS sensors, or metal oxide semiconductors such as tin dioxide (SnO2) on a sintered alumina ceramic bead contained within a flame arrestor, are one of the oldest and least expensive measurement technologies used in portable instruments. In clean air the electrical conductivity is low, while contact with reducing gases such as carbon monoxide or combustible gases increases conductivity. While MOS sensors can detect a wide range of contaminants, they have several shortcomings that limit their effectiveness: 1) Not benzene-specific unless used in sophisticated sensor arrays with pattern recognition; 2) Limited sensitivity, with detection limits usually in the tens of ppm; 3) A non-linear output, making them not particularly accurate. MOS sensors are at best gross indicators for toxic gases and vapors; 4) Relatively slow response; 5) Respond positively to moisture and temperature and can be poisoned and dirtied, and not easily cleaned.Gas chromatograph/mass spectroscopy lab analysis
In this method a gas sample is collected either by pumping through an adsorbent tube such as activated carbon, or by filling into an evacuated gas cylinder or Tedlar® bag. Sent to the lab, the sample is desorbed and analyzed with gas chromatography/mass spectrometry. This is the most sensitive and selective method available and is used as the standard for comparison. However, it is also the most expensive and time-consuming approach, typically requiring hours to several days before results are available.Portable GC systems
Portable gas chromatographs, usually with PID or FID detectors, provide selective benzene measurements down to 0.1 ppm, but have several drawbacks: 1) Tend to be heavy and bulky, making them difficult to use in tight spaces and on ladders and catwalks; 2) Relatively expensive and complex; therefore, usually only operated by an experienced industrial hygienist; 3) Sampling and analysis time is relatively long, similar to gas detection tubes (i.e., on the order of 5-10 minutes).Flame ionization detectors (FIDs)
FIDs work by burning a sample gas in a hydrogen flame. In this environment, organic compounds produce ions, which are measured on an electrometer. The resulting current is proportional to the concentration of organic vapor. The FID is very sensitive and linear over many orders of magnitude. Some of the shortcomings are: 1) It requires hydrogen and a mechanically stable environment for the flame, making the resulting instruments complex; 2) FIDs do respond to a broad range of organic compounds but are non-selective and therefore cannot measure benzene specifically unless connected to some type of separation system such as a gas chromatograph; 3) FIDs are expensive and maintenance-intensive, which limits their use in most industries.Photoionization detectors (PIDs) with compound-specific pre-filter tubes
While PIDs are broadband detectors, they can give a benzene-specific response by using a combination of a low-energy (9.8 eV) ultraviolet lamp and compound-specific pre-filter tubes such as benzene that remove organic interferences. This system provides rapid response down to 0.05 ppm in one minute with an accuracy of 10 percent in the 50 ppb to 5 ppm range. Measurements of STEL and TWA levels of benzene can be made in the presence of up to about 300 ppm of gasoline.The latest generation instruments give users the choice of a one-minute snapshot measurement or a 15-minute STEL measurement. The filter tubes also absorb moisture, so benzene-specific measurements can be made in steam vents.
Many monitors now include wireless data transmission for real-time detection from a remote source. The instantaneous feedback that these detectors provide enables workers to make rapid personal protective equipment decisions. And at the same time it allows them to perform their job tasks with a higher level of confidence knowing they are not exposed to hazardous levels of benzene.
References
U.S. Department of Health & Human Services: Agency for Toxic Substances and Disease Registry
Centers for Disease Control: NIOSH Pocket Guide to Chemical Hazards
U.S. Department of Labor: Occupational Safety & Health Administration, CFR29 and 1910
U.S. Department of Transportation Emergency Response Guide
U.K. EH40/2005 Workplace Exposure Limits, Table 1