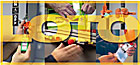
In the nearly 20 years since OSHA 29 CFR 1910.147,The Control of Hazardous Energy (lockout/tagout)was enacted, thousands of tragic incidents from hazardous energy sources have no doubt been avoided through application of the standard. Yet many accidents and fatalities still occur every year.
Compliance with the lockout/tagout (LOTO) regulation prevents an estimated 120 fatalities and 50,000 injuries each year, says OSHA. While this represents a significant improvement in employee safety, lockout/tagout is the most cited OSHA violation in manufacturing plants.
Having a highly visible LOTO program benefits both workers and employers through increased safety and productivity, and lower overall costs, which can include fines for non-compliance, lost productivity due to accidents, workers’ compensation claims, and even lawsuits. Let’s examine five key elements to an effective lockout/tagout program.
1) Risk assessment
Although 29 CFR 1910.47 is specific about minimum requirements, each employer has the flexibility to develop and maintain an energy control program that is specific to the needs of its particular workplace and the types of equipment used and maintained at its facility. Because each facility is unique, the first step in developing an effective LOTO program is to do a risk assessment.Whenever new equipment is added or reconfigured in the plant, conduct an assessment of potential hazard and potential personnel exposure. All plant system components and energy isolation points need to be documented. As things change, this documentation must be diligently updated.
2) Procedures in place
Next, LOTO procedures need to be put in place to ensure that all points at which there is potential for hazardous release of energy or personnel exposure are identified and isolated. The equipment or system must be at a zero energy state prior to anyone performing maintenance or repairs. Procedures should include a safe and systematic shutdown prior to isolation, and the steps necessary to put the system or equipment back in operation safely. Each procedure must identify all associated isolation point(s) and the correct LOTO device(s) to ensure that the isolation point(s) is/are inoperable and capable of maintaining a zero energy state in the system for the duration of the work.If the energy source can be locked out, then appropriate lockout devices should be installed. According to 29 CFR 1910.147, LOTO devices should be substantial enough that they cannot be easily removed without using “excessive force.” Tagout devices must be substantial enough to prevent accidental removal. If tags are being used, it must be demonstrated that they are equivalent to locks.
Some equipment has multiple isolation points; group lockout equipment is needed when more than one person working on the equipment must be protected from hazardous energy.
3) Documentation
Once LOTO procedures and equipment are in place, documentation is mandatory. Procedures for isolating and locking out hazardous energy must be readily available and highly visible to anyone coming into contact with the equipment or system. Posted procedures must be up to date, readable and protected from the environment by lamination or some other protective method.Employees must be instructed to leave the information with the equipment at all times. If electronic notification of procedures is used, then everyone involved must have access to a computer.
4) Training
An ongoing training program for LOTO procedures should be part of your plant’s overall employee training. All parties involved in working with equipment or systems with hazardous energy sources must be required to participate. Hold a briefing at each shift to familiarize everyone with the procedures and LOTO expectations. Discuss the consequences of not following LOTO procedures precisely.5) Inspection and audits
Periodic inspections and audits ensure that the implemented program stays current with the latest technology and best practices. This also helps you determine if the documented procedures are being followed.A way of life
An effective lockout/tagout program does more than just fulfill the letter of the law for 29 CFR 1910.147. It is an important investment in safety and in preventing downtime. The program should be reevaluated periodically to assess if changes or additions should be made.If employers treat lockout/tagout as a “way of life” in the plant, the program will be taken seriously and used effectively by those it is designed to protect.