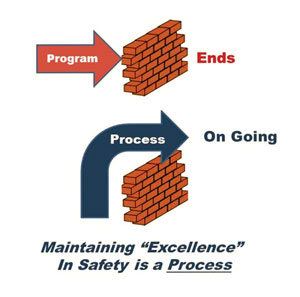
When looking at your safety culture, you must first determine “where you want to be.” How do you want safety to be perceived, valued and prioritized within your organization is the first question that must be asked. Once this is identified, an in-depth look at your culture as it exists today is critical.
These steps are best done by involving all management and primary employees to establish ownership. Everyone can help determine the best steps to affect any changes desired. Failing to engage employees in the safety process indicates a breakdown in leadership.
Leadership is more than directing the workforce and enforcing rules and regulations. Listening motivates and is far more important to good leadership than realized. If employees believe they are being genuinely listened to, respect and trust can be generated. By not listening to the ones who have to get the work done, managers and supervisors discourage ingenuity, motivation to take responsibility and active participation in solving problems.
Engage employees in decision-making
No one knows better than front-line employees what works best and what doesn’t work. Ask for input. Questions are possibly one of the most powerful tools of a good leader. Not all workers have the personality style to step forward with suggestions or potential problems. When asked, however, many will offer more than expected. This is especially true if they are convinced that their input is truly needed and wanted.
Limitations are too often placed on employee knowledge. Some managers and supervisors fall into the trap of thinking of employees as only a means of getting the work done and not contributors in determining how it gets done. Employees are often involved in outside-of-work activities that carry all the skills of problem-solving, leading groups and technical and organizational skills.
Measures must be developed
Traditionally, companies have relied on measuring safety using lagging indicators – results based on lack of bad results; lack of accidents or low number of accidents – things that have already happened.
Leading indicators can be derived by measuring safe and unsafe practices, collecting near misses for resolution – all preventative actions as opposed to reactive actions.
Reporting “Near Misses” is proactive and should not be punished. Potential accidents can be identified and corrections made before they become actual accidents and recordables. These activities attach value to success rather than failure. Always be prepared for the potential of increased reporting of accidents and unsafe conditions and behaviors. This is not a bad thing. It indicates a level of trust and commitment.
Change is never easy
|
People are predisposed to resist change; it threatens their sense of stability. People are creatures of habit and develop a comfort level with things as they are. Soliciting and using their ideas can make the transition a lot smoother. In developing a plan to maintain excellence in Safety Culture, the factors of natural change, technology and ideology must be considered and addressed as they occur.
It has long been established that people will do more when a positive consequence is attached to their efforts. Negative reinforcement, punishment, can stop a particular behavior for a while; positive reinforcement will foster more of the desired behaviors identified. The least expensive incentive available to management is recognizing and rewarding desired practice, behaviors and involvement in the safety culture process. Recognition, involvement and appreciation are positive ways to motivate employees to work effectively and safely. A simple thank you is quite effective. While rules and regulations must be established and blatant disregard for these must be addressed through disciplinary actions, positive reinforcement must be applied also.
Over time, we must go back to steps one through three. Establish where you want to be, verify where you are and involve all in identifying and implementing steps to get to where you want to be.
Footnote 1 “Developing Your Culture”, Donna Pearson Chadwick, April 1, 2009, http://ohonline.com/Articles/2009/04/01/DevelopingYour-Culture.aspx?p=1