1) What are respirator protection factors?
They're an expression of performance based on the ratio of two variables - the measured concentration of a contaminant inside the respirator facepiece cavity, and the measured contaminant concentration outside the respirator facepiece.The relationship between these two variables can be expressed not only as a protection factor (a number always greater than 1), but also as the penetration or efficiency. Protection factor assessments are made almost exclusively on human/respirator systems; penetration and efficiency assessments are made only on component parts of the respirator system.
Respirator protection factors are usually referred to as assigned protection factors, or APFs. OSHA says APF is the level of protection that a properly functioning respirator is expected to provide to properly fitted and trained users. An APF of 10 for a respirator means that a user could expect to inhale no more than one-tenth of the airborne contaminant present. The higher the APF, the greater the protection.
APFs, which appear in the NIOSH Decision Logic, the 1980 ANSI standards for respiratory protection and in all OSHA health standards, are based on quantitative fit testing (QNFT) or qualitative fit testing (QLFT), though QLFT only allows APFs up to 10.
Additionally, workplace protection factors (WPF) are a measure of actual protection provided in the workplace, and simulated workplace protection factors (SWPF) are a measure of protection using a lab simulation. The fit factor is another special application of the protection factor ratio that represents a quantitative measure of the fit of a particular respirator facepiece to a specific individual.
2) Where did protection factors originate?
The U.S. Bureau of Mines referred to the term "decontamination factor" in its Approval Schedule 21B, first issued in 1965. The bureau defined it to be "the ratio of the concentration of dust, fume or mist present in the ambient atmosphere to the concentration of dust, fume or mist within the facepiece while the respirator is being worn."
In 1975, OSHA and NIOSH jointly developed the Respirator Decision Logic, intended to ensure uniformity and adherence to proper respirator usage. It was updated in 1987, and since then various groups such as NIOSH, OSHA and ANSI have proposed factors for the different types of respirators available. OSHA is developing a new regulation to address the APF issue, but in the interim will recognize APFs declared in substance-specific standards, if applicable, or APFs granted by a specific OSHA interpretation, or the NIOSH APFs.
3) Why are APFs important?
APFs are essential to a proper respirator selection process. According to OSHA, in order to select an appropriate respirator you must:
- Conduct an exposure assessment to determine the type and amount of hazardous exposure.
- Take into account the factors that can influence respirator selection such as job-site and worker characteristics.
- Understand the APFs.
- Know the various kinds of respirators and their relevant characteristics.
The NIOSH Decision Logic criteria for selecting respirators is more specific:
- General use conditions, including determination of contaminants.
- Physical, chemical and toxicological properties of contaminants.
- NIOSH REL, or the OSHA PEL or other applicable exposure limit.
- Immediately dangerous to life and health (IDLH) concentration.
- Eye irritation potential.
- Any service life information available for cartridges and canisters.
The NIOSH Decision Logic contains three tables of APF classifications of respirators for protection against particulates, gas and vapor, and combination gas/vapor and particulate exposure. Through a series of questions, the logic narrows selection down to specific type of respirator listed on one of the three APF tables.
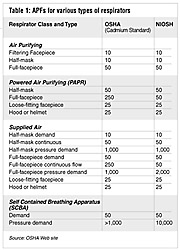
4) Why is there a problem with APFs?
While the NIOSH Decision Logic offers a very scientific process for selecting a respirator, that process will always be somewhat subjective. Individuals selecting a specific respirator must be knowledgeable about the limitations associated with each class of respirators (see Table 1) and must be familiar with the workplace environment.Another issue centers on determining APFs for a specific respirator. You basically multiply a respirator's APF (Table 1) by the exposure limit for the particulate, gas and/or vapor to which a person is being exposed. This number is the maximum use concentration (MUC).
There are exceptions to the basic calculations. APFs cannot exceed the contaminant's IDLH concentration, must account for oxygen-deficient atmospheres and must comply with substance-specific standards.
Different exposure limits also pose a problem. OSHA has its PELs (permissible exposure limits), NIOSH its RELs (recommended exposure limits) and ACGIH its TLVs (threshold limit values). For example, for chlorine, OSHA's PEL is 1 ppm, but the NIOSH REL is 0.5 ppm.
5) Why can't OSHA get everyone to agree on APFs?
They've been trying. In 1995, OSHA issued a ruling setting APFs, but later reopened the record based on the comments and controversy generated by that ruling.OSHA contracted with Mark Nicas of the University of California at Berkeley to prepare recommendations for evaluating protection factor studies and combining information across studies for use in setting APF values. Nicas' report, titled "The Analysis of Workplace Protection Factor Data and the Derivation of Assigned Protection Factors," was entered in Respiratory Protection Docket H-049 as Exhibit #156, and OSHA may use the report's recommendations as an aid to setting APFs.
The Nicas report recommends approaches to resolving science-policy issues related to setting APFs, including:
- Deciding which workplace protection factor studies should be evaluated;
- Accounting for particle size effects, respiratory deposition and below-detection-limit values; and
- Requiring specific statistical analyses to account for between-wearer variability in respirator performance, within-wearer variability, between-study variations and parameter uncertainty.
6) Didn't OSHA's 29 CFR 1910.134 resolve the APF situation?
No. This 1998 standard mandated employers to establish a comprehensive written respiratory protection program and new criteria for using chemical cartridge respirators, which eliminated the use of smell or taste by the wearer to help detect cartridge breakthrough. The odor test had also been part of the NIOSH Decision Logic respirator selection criteria. 1910.134 also required new fit testing protocols and fit testing for all tight-fitting facepieces.7) What must I do as an employer?
Follow and comply with OSHA's 1910.134 standard. NIOSH says you have three key responsibilities to your employees:
- Determine their exposure to hazards and continually sample the workplace to see if those hazards change.
- Fit test to assure a proper match between the respirator and the wearer.
- Randomly inspect your workforce's respirators to ensure they are being used and are in good condition.
8) What should we do about APFs pending a ruling from OSHA?
- Use the lowest exposure limit to choose a respirator using APFs.
- Select a respirator classified as providing a higher level of protection.
- Use the NIOSH Decision Logic.
- Comply with OSHA's 29 CFR 1910.34 whenever workers use respirators, whether on a required or voluntary basis.