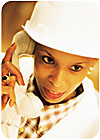
Whoa! That was close!!! I was inches from sliding right off the dock.â€
OK, how often does it happen to you? A fork truck and driver nearly drop four feet and you, the safety manager, know nothing about it. Near-miss reports are required at your facility, but how many have you received in the past year? Two? Five? None?
In the dark
Most safety practitioners know on a theoretical level that gathering information about all incidents, including near misses (or near hits, as some prefer to call them), is critical to adjusting the process. In the opening example, if there are several reports of sliding fork trucks on the dock, investigation might find a slick on the floor from a leaking oil seal. Fork truck maintenance becomes suspect. In the end, it’s found that management had to cut maintenance costs.But if you’re operating in the dark, lacking a meaningful history of near-miss events, you’re wasting precious time. You’re left committing scarce time and resources to random, isolated — but more serious — incidents and addressing only symptoms.
Statistical noise
In the average 100-person company, the BLS data for 2004 suggests there might be five OSHA recordable cases a year, and perhaps two of those will involve lost time. But in one year, total recordables might be at eight and drop to three the following year and land on the average five the third year. In all cases you have statistical noise, not statistical significance. You simply can’t manage a process on such a small handful of data points. You need more information — and the only way to get it is to have successful total incident reporting.Meaningful input missing
An informal survey of my clients and associates for this article found that about 80 percent of respondents ask for first-aid cases, property damage reports and near misses. But only around 20 percent get any meaningful input — and four of those are OSHA VPP sites.Leading the pack on total incident data was one organization with an OSHA recordable to total reports ratio of 1:54! In other words, in this organization 54 incident reports were received for every OSHA recordable. Another firm reported a ratio of 1:27. The ratio for all surveyed organizations was 1:11, but the leaders skewed that sharply. Most organizations were struggling in the range of one incident to three or four reports. Plus, the bulk of reports were property damage and first aid — events that tend to get noticed and therefore reported.
As important as total incident reporting is to the safety process, the reality is that few organizations try it and even fewer do it successfully. Most safety practitioners and their management and the people on the floor are all working long hours trying to do too much work as it is. They fear that yet another good idea such as total incident reporting will break the camel’s back. Those that do make it work realize the effort they put into it helps prove the adage “safety pays.â€
It’s also instructive that OSHA VPP organizations tend to lead in this area. Comprehensive reporting of all types of safety-related incidents is a cultural and process issue, not a simple reporting compliance problem.
Making a reporting system work
So how do you make it work?There are three stages for total incident reporting. One follows the other. Stop after stage one and you won’t see any reports.
First, establish a clear expectation that reports must be submitted. Then, create a simple reporting process that is workable and sustainable. Finally, build the process into the workplace culture and base the effort on mutual trust.
12 tips to increase reporting
To work through the stages and succeed at getting into the range of reporting ratios you saw above, consider these tips:-
Broadly define “near miss.â€
Essentially, it’s any event, condition, action or situation that could have resulted in injury or loss but for timing and/or distance. In the example at the start of this article, a few inches made the difference. If a mower blade throws a rock at 9:00 am rather than 7:55 am when everyone is walking in to work, it’s a matter of timing. -
Make sure everyone in your organization knows — and supports — the near-miss rule that “more is better!â€
When people report near misses, they are helping the organization. They are involved. They’re doing good — even if the near miss was because they lost focus for a second or failed to follow a safety rule.
We all know by now momentary lapses in safety are not simple failures; they are tied to the system and the culture. By reporting something to which they may have contributed, employers, supervisors and managers are really opening the window for us into the organizational culture — that’s what we want and that’s good. -
Educate everyone on the logic of total incident reporting and the process to follow.
They need to buy in rather than be told what to do. -
Address the question “what’s in it for me?â€
For everyone — you, managers and supervisors, and line employees — it’s easy to see only more work, or problems with a comprehensive reporting system. In fact, having an effective process beats brush fire-fighting. It provides data that allows you to see the big picture and focus on real root causes. It keeps people from getting hurt. For everyone, it’s the “feel good†of an appreciative comment or successful solution. -
Make it a “no fault†system.
No discipline, no written warnings, no embarrassment — but lots of “thank you’s†and management reinforcement. Get excited about the input enough times and people will believe that they really are doing something good by making reports. Keep repeating: “near-miss reports are good — no one has failed.†In one company, the only penalty is for not reporting injuries. -
Keep it simple.
No one wants to jump through hoops to make a report. One of my VPP associates uses a green card system to report everything (hazards, near misses, etc.) and another has a safety improvement opportunity form.
Make notes — send it in — it’s that simple. Others use a company intranet or e-mail. One organization has the supervisor interview the reporting employee to get all the facts, lessening the load on the employee. -
Use near-miss reporting as a safety metric.
Near misses are leading indicators; injuries are trailing indicators. Set an increasing ratio of recordable cases to near misses as the annual target. If recorables go down while the ratio goes up, that’s a very positive metric. And the sky is the limit. One report per employee per week would be fantastic. -
Ensure a fast response.
Hold supervisors to 24 hours maximum to provide feedback to the submitting employee (and reinforcement for using the system. -
Follow up on every report.
But concentrate improvement efforts on those cases with a high or medium potential for injury or damage the next time. -
Get everyone involved in solutions.
If you’re getting a high volume of reports, that tells you people are interested and it tells me that they’ve got ideas to share. -
Focus on long-term system fixes.
By fixing the system rather than the problem, you ensure related issues will be resolved. -
Use feedback.
Tell everyone about how the system is working. Share numbers and costs. Show how safety improvements came from near-miss reports. Remember, success breeds success. And be sure not to “burn†anyone. Trust in this system is critical. If someone gets written up, or fired, or blamed, or brushed off, word of that will travel fast and kill your process overnight.
As with so many other tools and techniques, total incident reporting works if management and employees and the company culture support it. If you’re still having trouble convincing anyone that OSHA regulations should be followed, work on fixing the culture and save total incident reporting for some other time.