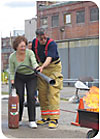
Saint-Gobain worksite chose activities to express each site’s own personality and address site-specific issues.
Directing the attention and energy of 200,000 people working in 50 countries around the world at one time on the topic of industrial health and safety is no easy task. It takes planning, coordination and, most importantly, the initiative and ingenuity of the employees in each individual facility. And that is exactly what the global industrial manufacturer, Saint-Gobain, did this past summer.
The company celebrated its second International Health and Safety Day by focusing on three simple goals: zero work injuries, zero occupational illnesses, and zero non-recovered waste. Any EHS pro will agree that those are quite lofty goals. But the company has set that bar for itself and will continue to reach for it through its EHS efforts.
Global EHS efforts at Saint-Gobain have improved dramatically in the last 15 years. In the early ’90s, the company had an average rate of 40 injuries per day; today that number has dwindled to six. But Saint-Gobain acknowledges that there is still a long way to go to reach the ideal number of zero. The company sees health and safety as not only a corporate moral obligation and every employee’s business, but also as a necessity for top industrial performance and economic success.
Executive endorsement
To communicate the overall corporate message, Saint-Gobain created and globally distributed an Environment, Health and Safety Charter. The company also developed a DVD that was distributed to and shown at every one of the hundreds of plant and office locations around the world on June 13 of this year. In it, Chairman and CEO Jean-Louis Beffa and Pierre-André de Chalendar, COO, addressed employees in various languages about the strong determination of the company to eliminate workplace injuries.The DVD also featured an impassioned message on the essential nature of EHS awareness and its role in the company’s profitability from Jean-François Phelizon, president and CEO of Saint-Gobain Corp. (SGC), Saint-Gobain’s holding company for its U.S. and Canadian businesses. SGC has one of the best overall safety performances within the parent company worldwide. At least 60 percent of SGC plants had no lost-workday injuries in 2005; the lost-workday case rate improved by 28 percent; and the recordable incident rate improved by more than 10 percent. Much of that was attributed to strong executive endorsement of the EHS concept, led by Phelizon.
With the DVD and charter as common tools, the company allowed each site to decide the most effective and creative way to observe the day at its own location, addressing the particular needs and concerns of each plant and office. General managers, plant managers, EHS officers and human resources managers, where appropriate, planned and implemented the day’s elements.
Many of the ideas generated at the first International Health and Safety Day that took place in 2004 have since been initially developed. Many sites took what they learned and built on it, even borrowing ideas from other Saint-Gobain sites. (See “Innovative Ideas†sidebar.) SGC had communicated to all employees the success of the 2004 event and encouraged an exchange of ideas for the next observance. Corporate newsletters and a poster created in the Paris headquarters showed highlights of activities that happened throughout the world. Similar communication plans are underway to spread the word among the 200,000 employees about the most recent day’s success.
Positive impact
Chris Scholl, director, health, safety and environmental affairs for Saint-Gobain’s High-Performance Materials businesses, was closely involved in the first and second International Health and Safety Day observances. “I think it was a very good thing with a lot of value for the employees and the company,†he said. “By diverting the time of employees from their production responsibilities and other support tasks, we’re communicating the seriousness of the culture of safety. That’s not to say we didn’t have fun doing it. Those plants that made the day fun were the ones that probably did a better, more memorable job of communicating the message than those who may have had only classroom training.â€â€œEach site really has its own personality,†added Scholl. “By giving them the leeway to do things the way they chose, they were able to express that personality and address the issues that are important to them.†He noted that in Worcester, Mass. — where Saint-Gobain has seven plants — each site had its own agenda of activities, and then there was a centralized open house for all employees to visit. “You have 1,500 people who were given time to attend the open house and the majority of them took advantage of the opportunity. That says a lot about what they felt about the value of the day,†Scholl said.
Phelizon enthusiastically supports the concept of the International Health and Safety Day for a very practical reason, in addition to the corporate responsibility of assuring employees that they will return home safely to their families from work.
“All successful manufacturing operations should be able to trace their success and profitability back to a very strong emphasis on safety within each plant,†said Phelizon. “At Saint-Gobain, we see that a plant with a poor or even mediocre safety record is not a very good plant. Bad financial results can be directly connected to an unimpressive safety record. That’s because a strong adherence to safety, or lack of it, shows the level of dedication the workers have for their work.â€
Saint-Gobain is looking ahead to its next International Health and Safety Day as a way to continue communicating the message that safety is an overall lifestyle behavior, whether it is wearing a seat belt, driving slower, wearing safety glasses, or operating a forklift properly. And the company hopes to increase the number of locations that have achieved one-million employee hours worked without a lost-workday injury. “It’s really not utopia,†said Phelizon. “We know it can be done.â€
Sidebar 1: Innovative Ideas
Here’s a list of some of the more unusual activities that took place throughout the U.S. and Canada. EHS professionals planning similar widespread health and safety days could use this list to jump-start the brainstorming process:- Safety “Jeopardyâ€-type board game
- Skin sun damage analysis
- Hands-on fire extinguisher training
- “Healthy Alternatives†picnic with veggie burgers, turkey sausage, frozen yogurt, etc.
- A “10,000-step†program encouraging a “walk†as far west as a sister plant in California
- Remote control forklift with simulated warehouse floor to promote equipment safety
- “Needle-less†acupuncture demonstration for pain relief
- Rape and abduction prevention clinic by local police
- Massage therapist and chiropractor examinations
- Truck rodeo
- Rewards of $1 “Saint-Gobain Bucks†to employees wearing safety belts
- A moment of silence in remembrance of all injured workers
- Sleep apnea screenings
- Bone density screenings
- Defensive driving training
Sidebar 2: Planning a Health and Safety Day
- Communicate strong support for the observance from top management.
- Keep the message simple: zero injuries, zero occupational illnesses, and zero discharge.
- Give general outlines on how each site should observe the day.
- Let each facility express its personality and needs by the activities it plans.
- Try to make activities fun and creative, and encourage involvement.
- Bring contractors, vendors, community groups, and local businesses to the event.
- Give equal time to safety and health at home.
- Share information with all sites on how each chose to observe the day.
- Keep health, safety and environmental affairs top-of-mind for all employees at all times.
- Schedule meetings after the event to review and evaluate each location’s progress.
- Aim for perfection.