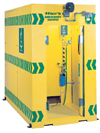
In today’s litigious society, you’ve got to stay on top of your game to avoid becoming entangled in proceedings aimed at assigning responsibility for physical harm associated with workplace injuries. If a lawsuit can be filed (and won!) based on a vendor supplying a cup of coffee to-go that is “too hot,” imagine the legal implications that might be associated with a major industrial spill or splash accident.
Emergency equipment
It’s interesting to note that ANSI Z358.1, the standard that applies to emergency showers and eyewashes, does not specify the number or specific placement of emergency response assets. It, in fact, leaves the decision as to number and locations up to each facility. Direction is simply provided as to the general placement (within ten seconds walk from any potential accident site, on the same floor, with no obstructions in the pathway).If the selection task isn’t difficult enough using that criteria, consider the possibility of multiple simultaneous victims attempting to use showers concurrently. It’s one thing waiting for your kids to finish showering in the morning before school and work. Now, imagine waiting around to use a drench shower because you were just doused with a very aggressive caustic solution and you weren’t the first victim to get to the shower. That circumstance is also covered by the standard, saying that sufficient assets must be available.
Multiple simultaneous use
But wait… there’s more! Lest you believe that we’re talking about only the number of showers and eyewashes available within a ten-second, unimpeded walk along the same floor from an accident site, consider the output requirements of multiple simultaneous use. Each shower must provide for a flow of 20 gallons per minute for a full 15-minute use cycle, while each eyewash must have a flow of .4 gpm and each eye/face wash 3.0 gpm for the same 15-minute duration. So, the more showers and eyewashes you actuate simultaneously, the more total system pressure and volume required to maintain the flow rates of each outlet.And, finally, the 2004 revision of Z358.1 clarifies the earlier requirement for tempered water. Prior to this most recent revision, tempered water was required — however, the definition of tempered called for “tepid,” which was open to interpretation. In 2004, tepid was defined as between 60ºF and below 100ºF. So, each facility must provide accommodations for the “correct” number of showers and eyewashes (without further direction), in the correct locations (with some general definition) and those assets must provide water in the proper flow rates (regardless of the number of simultaneous victims participating in the system) for the full 15-minute use cycle… and, that output water — every drop of it — must be tempered to the between 60ºF and below 100ºF definition of tempering. Phew!
No pressure, but errors in the selection of shower/eyewash components or, more importantly, the design of an integrated emergency response system to adequately supply water to it can result in more significant injuries for victims and/or liability for those who designed that system. Consider the real possibility of being asked to provide the reasoning why a specific decision was made in interpreting the ANSI guidelines or in selecting a specific product versus another design. Or, how about being put on the spot about how you assured that the maximum demand for properly tempered water could be met system-wide for a large number of showers and eyewashes?

This engineered solutions schematic shows a tempered-water network that can be designed to address a specific facility’s emergency equipment systems needs.
Source: Haws Corporation
Source: Haws Corporation
Specific needs
Providing matched and balanced emergency equipment systems is a specialty that we call Engineered Solutions™. Engineered Solutions™ are designs that incorporate the specifically sized components needed to address a specific facility’s needs and possible peak demands. Emergency equipment manufacturers are the best source for detailed understanding of the complexities and capabilities of their products, and, more importantly, are in the best position to assist in determining how to “string” those products together with booster pumps, tempering and recirculating systems to make a foolproof installation. Also, because emergency equipment manufacturers build these systems every day, they can advise clients on current best practices and cost-effective approaches used in other similar facilities.These days you can’t be too safe! That applies equally to the safety precautions in your facility, your preparations for any eventuality, and “safe” as it applies to assuring that you are doing the best job for your employees, while also safeguarding against claims of negligence in your specification process.