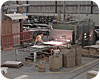
OSHA requires that manufacturers and importers provide chemical hazard information to employers and workers. Under the Hazard Communication Standard (HCS), employers and workers need access to information on the hazards of all materials produced or used in the workplace so they can protect themselves.
The HCS also applies to hazards from potential combustible dust situations. In fact, the HCS is the most frequently cited standard with respect to combustible dust related hazards.
Dust dangers
What makes dust explosions so destructive are the secondary explosions. The initial event disturbs accumulated dust, which disperses into the air. If this new, larger dust cloud ignites, it results in one or more secondary explosions that can be far more destructive than the initial event due to the increased quantity and concentration of dispersed dust.
A 2006 report from the Chemical Safety and Hazard Investigation Board (CSB) detailed nearly 280 dust fires and explosions in the U.S. over the prior 25 years -
resulting in 119 fatalities and over 700 injuries.
Most disturbing, in many of these incidents, workers and managers were unaware of the potential for dust explosions or failed to recognize the serious nature of dust accumulation hazards.
What is combustible dust?
OSHA defines combustible dust as a solid material composed of distinct particles or pieces, regardless of size, shape, or chemical composition, which presents a fire or deflagration hazard when suspended in air over a range of concentrations. Any combustible material, and some materials which are not normally considered combustible, can burn as rapidly as dust when dispersed in air.
In general, combustible dust particles have a diameter of less than 420 microns (those passing through a U.S. No. 40 standard sieve). However, larger particles can still pose a deflagration hazard - for instance, larger particles can abrade each other as they move around to create smaller particles.
Different dusts of the same chemical material can have different ignitability and explosibility characteristics depending upon particle size, shape and moisture content. These physical characteristics can change during manufacturing, use or while the material is being processed.
OSHA actions
On October 18, 2007, OSHA initiated a Combustible Dust National Emphasis Program (NEP) to target facilities that create or handle combustible dusts, including wood products, food products, metal products, chemicals, pharmaceuticals, rubber and plastic products, paper products, furniture, electric and sanitary services, transportation equipment, durable goods and textile mills.
Under the NEP, OSHA has conducted more than 1,000 inspections and found more than 4,900 violations for combustible dust and other hazards.
OSHA is also gathering information to address combustible dust through rulemaking. OSHA plans to launch a small business regulatory review panel in 2011. Currently, OSHA does not have a comprehensive standard on combustible dust issues. The agency addresses combustible dust under various existing standards, such as HCS, ventilation standards and general housekeeping standards, as well as the General Duty Clause.
Hazard analysis
Not all manufacturers and importers are aware of combustible dust hazards, nor have they all considered the combustible dust hazards of their products. However, any product that can create combustible dust when processed would fall under the HCS.
The HCS requires chemical manufacturers or importers to consider potential exposures of their products that may occur under normal conditions of use or in foreseeable emergencies and to address those hazards on the Material Safety Data Sheet (MSDS) and, where appropriate, on the product label.
OSHA considers operations or material processes that generate dusts to be normal conditions of use. These include abrasive blasting, cutting, grinding, polishing or crushing of materials; conveying, mixing, sifting or screening dry materials; and the buildup of dried residue from processing wet materials.
Employers must also consider workplace conditions and assess the potential for dust explosion in equipment such as dust collectors and other locations where dust can settle, both in occupied areas and in concealed spaces. A thorough analysis will consider all possible scenarios in which dust can be disbursed, both in the normal process and potential failure modes.
Labels and MSDSs
Most employers rely on the hazard determinations performed by chemical manufacturers and importers. However, not all manufacturers and importers have considered the combustible dust hazards of their products.
If the downstream use or processing of a product routinely generates combustible dusts, the manufacturer or importer must include warnings about potential explosion hazards either on the product label or on the MSDS.
OSHA says that the container label is intended to be an immediate visual reminder of the hazards of a product, so every hazard does not have to be listed on the label. Employees are to be instructed to look to the MSDS for more complete hazard information.
Employers must have an MSDS for each hazardous chemical that they use and ensure that MSDSs are readily accessible to workers. The MSDS must include precautions for safe handling and use, as well as control measures such as engineering controls, work practices or personal protective equipment. The MSDS may list combustible dust hazard information in the section for:
- Hazard identification
- Fire fighting measures
- Accidental release measures
- Handling and storage
Training and information
HazCom requires that employees receive information and training on workplace hazards so that they can take the appropriate steps to protect themselves. Employers using materials that could create combustible dusts must evaluate those operations and tasks where dusts are present or may be generated and explain to employees the potential hazards and what employees can do to protect themselves.
All employees should be trained in safe work practices applicable to their job tasks, as well as on the overall plant programs for dust control and ignition source control.
Are you in compliance?
OSHA found during NEP inspections that only 18% to 22% of facilities inspected were in compliance. The average number of violations per NEP inspection is 6.5 as compared to 3.1 for the other inspections.
The total citation penalty amount OSHA has proposed under the Combustible Dust NEP is $14,848,686. The average penalty proposed per serious violation during combustible dust NEP inspections is $1,233 for Federal OSHA.
If your facility handles agricultural products, wood, coal, coke, biosolids, sugar, paper, soap, metals like aluminum and magnesium, textiles or plastics, you could have combustible dust hazards and could be subject to OSHA inspection under the combustible dust NEP.
With OSHA becoming more active and hiring more compliance officers, we can assume that OSHA will continue to take strong enforcement actions to address combustible dust hazards.
SIDEBAR: How Dust Explosions Occur
The familiar fire triangle is made up of: oxygen, an ignition source and fuel. All three conditions must be present for a fire to start.
The “dust explosion pentagon” adds two more conditions: dust particles and the confinement of the dust cloud. Similar to the fire triangle, if one part of the pentagon is missing, a combustible dust explosion cannot occur.