The ANSI/ISEA 138:2019 standard fills a critical gap in the industrial glove standards infrastructure. One question often asked by end-users is: what performance level is appropriate for application needs? This question is not unique to the dorsal impact glove standard. This article will discuss how impact is measured to provide context for end-users to determine the appropriate impact performance per the ANSI/ISEA 138:2019 dorsal impact glove standard. When assessing the appropriate dorsal impact glove is it critical to conduct a hazard assessment and obtain guidance from a certified industrial hygienist or safety engineer
Impact considerations
Consider this example: Shoot an armor piercing bullet at a brick wall and it will likely pass through. If a baseball were hurled at the same wall with the same kinetic energy of the bullet it would bounce off. The difference in outcomes in these two examples is due to the significant difference in impact areas of the ball vs. the bullet – where a smaller contact area translates into a much higher concentration of energy. And the fact that the bullet is several orders of magnitude harder than the ball.
This example highlights that, when evaluating impact forces, it is important to consider two important factors:
- Contact area
- Hardness of the materials involved in the impact
Not only do we need to consider the total energy of the projectile (5 Joules for the ANSI/ISEA 138:2019 impact test method), but the concentration of energy at the contact area.
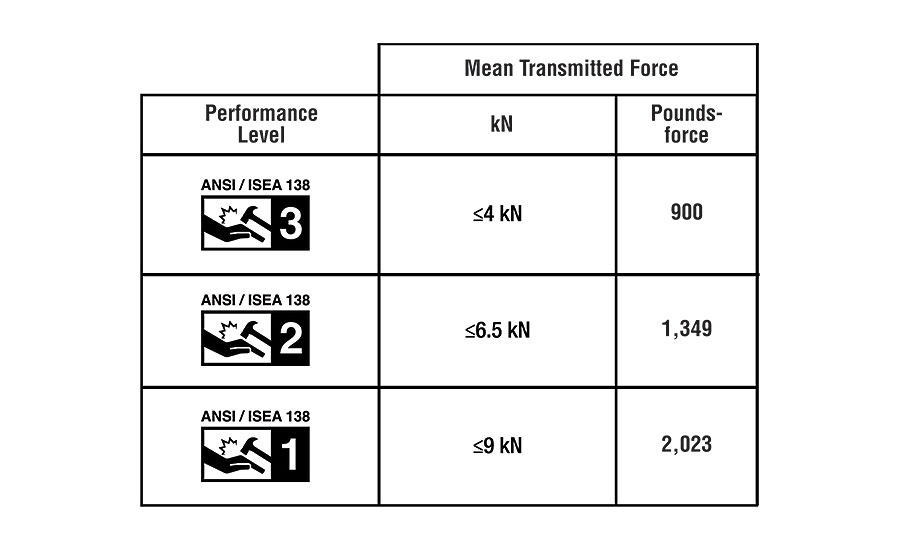
In other example, a pro can throw a football (about 0.88 lbs.) at about 70 mph generating about 190 joules of energy. That is about the same amount of energy from the firing of a .22 caliber round (0.006 lbs. at 850 mph). But, would rather be hit by the football or the bullet? Keep in mind that the ANSI/ISEA 138:2019 test method calls for a solid metal striker that has a 2.5kg (5.5 lb) mass (“weight”) with a contact area of 3.15 inches in diameter.
Impact measurement units
Another challenge in interpreting impact force results from the ANSI/ISEA 138:2019 impact standard is the, often, unfamiliar terms used. The SI system (International System of Units) - the modern metric system of measurement is the dominant system of international commerce, trade and science. The ANSI/ISEA 138:2019 impact standard utilizes SI system units for force and energy.
The force unit in the SI system is the newton (symbol: N). 1 newton (N) is equal to 0.22481pounds-force. Typical impact forces encountered in ANSI/ISEA 138: 2019 compliant testing are over 1,000 newtons. To simplify, in the SI system a thousand is abbreviated as “kilo” such that 1,000 newtons = 1 kilo newton (1 kN).
The corresponding energy unit in the SI system is the joule. It is an expression of the mechanical work done by pushing an object through a distance against a force. The English unit of energy is the foot-pound. 1 joule is equal to 0.737562 foot-pounds. The test method utilized in ANSI/ISEA 138:2019 is designed to generate 5 joules of energy.
The table provides the transmitted forces for performance levels in the SI system as well as the corresponding English units.
Impact examples
The graphic provides examples of impact scenarios. These examples are for illustrative purposes only. Keep in mind that the contact area and hardness of the materials involved are different for each example. The goal here is to provide general orders of magnitude to serve as a frame of reference for ANSI/ISEA 138:2019 performance levels.
Remember that the dorsal impact glove standard measures transmitted forces measured after a portion of impact energy has been absorbed by the glove material being tested. The maximum impact forces generated with a metal-to-metal (no glove sample) impact in a drop rig is around 45kN (10,116 lbs-force).
The ANSI/ISEA 138: 2019 dorsal glove impact standard can be a powerful tool to improve hand safety performance. End-users must carefully assess the appropriate impact performance level for their applications needs and solicit the expertise of an industrial hygienist or safety engineer.