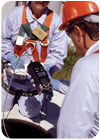
Gas detection equipment usage and maintenance complexity is considered high. For usage, products require basic understanding of hazards (gas stratification and subsequent sampling techniques), action steps upon alarm, and comprehension of display (gas readings, battery life, etc.) no matter how simple the operation is. For maintenance though, the level of complexity can be even higher. Tremendous infrastructure is often necessary to ensure proper management of function testing and calibration procedures, documentation, calibration gas materials management, instrument maintenance and repair. This infrastructure can grow exponentially as the number of sites using instrumentation increases: users increase, routine parts purchases vary, maintenance methods and regularity vary, and documentation is decentralized.
The evolution of gas detection vendors to serve the needs of their customers can be traced across three eras. The first spans the historic period of gas monitoring up to the mid-1990s. The second era occurred from this point until today. We are now embarking upon a third era, one in which technology is being tuned to offer unparalleled capability for improved safety, reduced cost and better compliance for gas detection users.
The first era
Until the mid-1990s, gas monitoring manufacturers had not been capable of adding much process value to customers. The maintenance and ownership logistics for the first mine safety lamps were not too different from the instruments available in the 1990s. While instrument functionality evolved to make things easier for customers (for example, push-button versus potentiometer calibration), virtually no advancements were made in delivering better solutions for customers who were solely responsible for managing usage and maintenance.The second era
Over the last decade, gas detection manufacturers have sought ways to reduce complexity by offering accessories that automate troublesome tasks such as function testing, calibration and recordkeeping. Calibration stations can simplify equipment maintenance. Many users have migrated to an automated calibration and function testing solution, delivering better process performance and lowering costs. These systems, however, have not been able to deliver a comprehensive solution to users seeking complete maintenance process excellence, as much of the responsibility still rests with them.
Groundwork for third era: DRM
The Internet has opened the door to enable unparalleled communication ability between companies. A trend emerging from this is device relationship management, or DRM, which allows aware, connected devices to reach a central “brain†and communicate information, diagnostics, component status and other valuable information.At baseline, this information is highly valuable when it is able to initiate actions delivering proper material management, timely service and product uptime; within the context of safety applications, these efficiencies are icing on the cake after ensuring process excellence leading to higher levels of safety.
Gas detection equipment has emerged as a likely candidate for DRM. As stated earlier, it is a product with relatively high complexity of maintenance and use, and it also has high intelligence. Product lifecycles are commonly two to five years and can be a significant operating expense for a plant site, and can run into the millions of dollars for large corporations.
Third era programs
“Third Era†gas detection is characterized by technology delivering greater employee safety and operating efficiency. The automation of “second era†systems enabled users to see improved gas detection programs in the following areas:- consistent calibration and function testing practices;
- consistent documentation; and
- reporting on component failure.
- Proactive service solutions — Should diagnostics determine a component failure, Third Era systems take steps beyond simple notification. Proactive service solutions are initiated to remedy the situation. Factors such as customer choice, capability and location will determine whether a replacement part is shipped, a replacement unit is shipped or a service technician is dispatched. Regardless, certain steps are removed from the user; determining what needs to be done, finding and maintaining qualified personnel to perform maintenance and repairs, and taking steps to remedy the situation all move from the user to the service provider.
- Enhanced system reporting — In addition to providing instrument status and calibration/function test dates, current Third Era solutions enable users to receive reporting via email on the state of the overall system. Previously invisible but valuable data, such as the lot number, gas constituents and expiration date of calibration gas cylinders, is now able to be programmed on smart chips attached to the cylinder and transmitted to the service provider.
- Networking — Multiple sites can be connected through one system, allowing for responsible parties to consolidate programs and have visibility (of both system status and cost) at a higher level.
- True outsourcing — Comprehensive service offerings coupled with hardware provide true solutions that enable users to outsource the management of their gas detection, leaving the user with only the responsibility of instrument usage.
- Product on demand — Users employing a Third Era solution have a dramatically simple way to add product for either short-term (weeks to months) or long-term needs. Instruments can be easily moved onto or out of a contract, depending on monitoring requirements.
- Supply contract versus purchasing — With a comprehensive service/supply contract, pricing is determined simply on the final instrument needs. No further ordering is necessary when parts requirements arise; these are simply addressed as a component of the existing contract, further simplifying procedures and ensuring proper channels are followed.