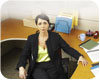
Don’t ignore a lone IAQ complaint.
Due in part to the lack of clear regulations, elusive trails of evidence, and the disparity in reported symptoms by employees, indoor air quality (IAQ) issues are often relegated to the “10-foot pole” department by non-industrial hygienists.
After all, who wants to respond to a lone complaint about “toxic air” when the other 50 employees in the same work area are fine? Still, with a little pre-planning and strategic action, even the most reluctant among you can perform an effective IAQ assessment that just may soothe even the most agitated workers.
Looking for clues
As with nearly any other safety strategy, the role customer service plays is crucial. In many instances, an IAQ complaint is reported after the employee is “symptomatic.” At this point complaints can vary from feelings of a cold or flu to a full-blown allergic reaction.
The safety professional is already at a disadvantage because the leverage of preventive action has been lost. It is also more difficult to explain the possibility that the employee really does have a cold or flu rather than having to agree, at least in the short term, with the employee’s conclusion that he is experiencing something far more serious.
Still, all IAQ investigations must be taken seriously, no matter how crazy they sound, until a solution can be offered.
Presuming you already have some prior knowledge of what to look for in the way of the physical signs of IAQ problems, your assessment should naturally begin with a visit to the work area where the complaint has been reported. Your first stop should be with the supervisor of the work area to let him or her know why you are there and to explain your plan of action.
I find good results by practicing the following:
- Interview the originator of the complaint first.
- Interview co-workers who share the same work space.
- Ask for specific examples of what they are experiencing.
- Ask them what is different than before.
- Ask them what they expect to be changed.
- Be a good listener.
- Be attentive and supportive.
- Maintain communications.
- Finish what you start.
Using IAQ monitors
If your budget allows, another helpful tool is a portable indoor air quality monitor. When planning your purchase, I suggest you consider units that have the following monitoring features:
- Temperature
- Humidity
- Carbon dioxide
- Carbon monoxide
- Volatile organic compounds
IAQ monitors are generally easy to use. What’s more, they are quite accurate and in just a few hours provide a “snapshot” of the condition of the air in any given sampled area.
Not as accurate as IAQ monitors but less expensive are “colorimetric” tubes that can collect short-duration samples that might indicate areas needing further attention. Colorimetric tubes can also be used to test for air contaminants that are not usually included with IAQ monitors, such as formaldehyde and ozone.
Make friends with the facilities department
Many IAQ issues can be resolved by simple heating, ventilation, and air conditioning (HVAC) modifications. This is where having a good rapport with your facilities department or building manager can come in handy. Use their expertise in troubleshooting, especially in cases where your previous monitoring has indicated such conditions as extremes in temperature and humidity, and elevated carbon dioxide (ex. > 1000 ppm – 1200 ppm).
Perceived issues vs. valid ones
The most important element of the IAQ assessment is determining the difference between a perceived issue and a valid one. When feasible, it is best to move the affected employee or employees to a different work location until a determination can be made. While this may sometimes sends a message to employees that there really could be a problem, you can end up smelling like the proverbial rose if it turns out there truly is a condition that needs to be corrected.
In a nutshell, while the non-industrial hygienist may be reluctant to get involved with IAQ issues, there are a number of low-cost strategies and smart investments where they can be successfully managed without the expense of hiring a consultant. In the present climate of cost-cutting, this can only increase your value as a safety professional.